Industrial Ventilation Fan Selection – Part 2
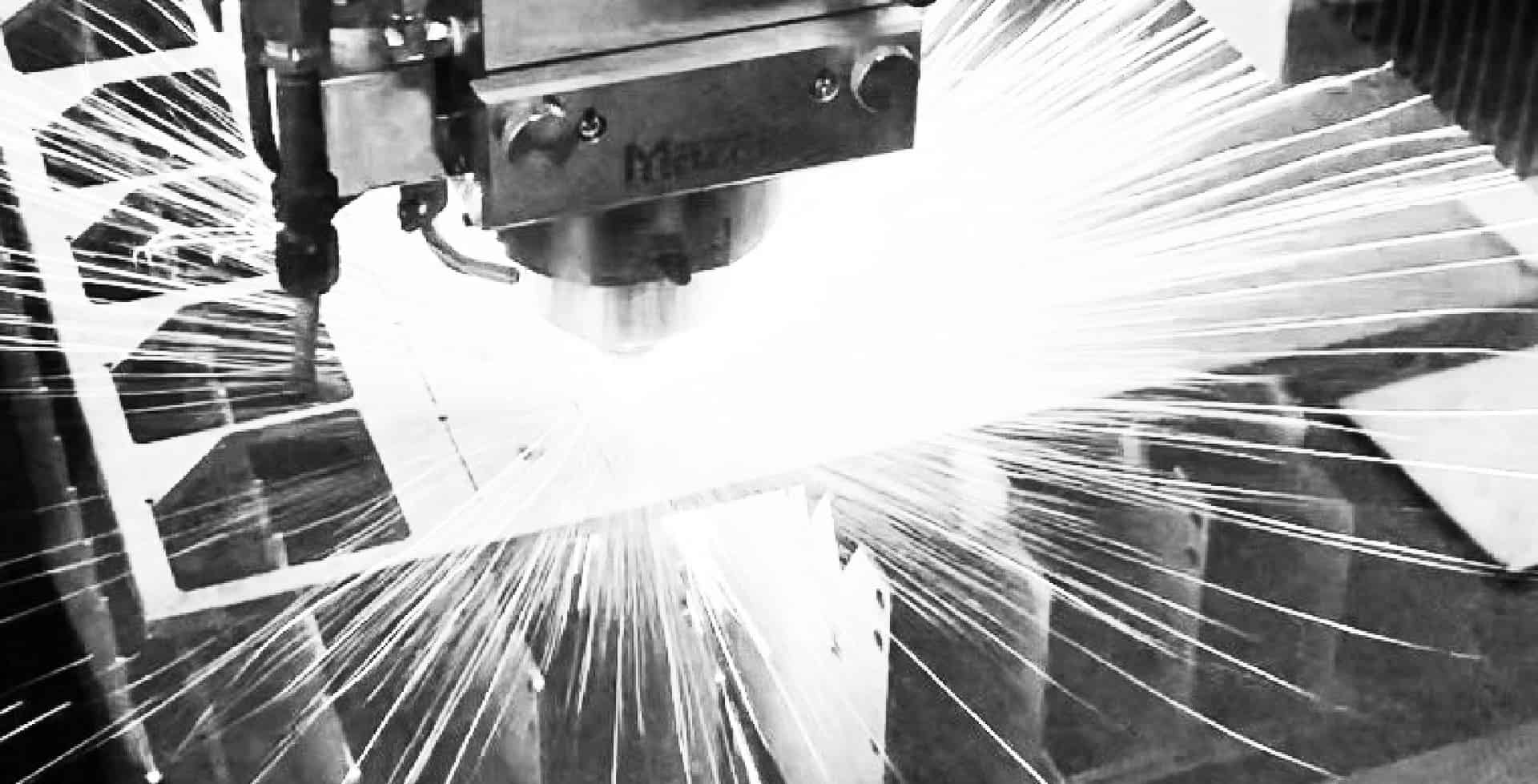
As explained in “Industrial Fan Selection – Part 1” a fan is the primary air moving device in an industrial dust collection system. Part 1 defines fan types and ideal applications. In Part 2, the primary considerations for selecting the right fan are defined.
However, as recommended in the Industrial Ventilation: A Manual of Recommended Practice for Design, “the exact performance and limitations of a particular fan should be obtained from the original equipment manufacturer.”
Considerations for selecting a fan
Selecting a fan for an industrial dust collection system requires more than selecting the fan type. Other characteristics such as the airstream, operating temperature, drive arrangements and mounting, as well as those listed below, should also be considered.
Capacity
- Flow rate: The flow rate is based on system requirements. The flow rate should be specified as ACFM or SCFM. The air temperature, fan elevation, moisture content and other air density factors need to be provided to the fan manufacturer.
- Pressure requirements: The Fan Static Pressure (SP) or Fan Total Pressure (TP) based on the system pressure requirements. A system pressure drop calculation should be completed to determine the SP and TP values.
Airstream
- Material handled: If there is particulate or moisture in the air stream, the right fan wheel or blade needs to be carefully selected and depends on what is being conveyed. Build up or corrosion of fan wheels can lead to safety concerns, decreased performance and bearing failure due to imbalance.
- Explosive or flammable material: Always refer to the standards of the National Fire Protection Association and other governmental regulations when dealing with explosive or flammable materials. If there is a risk of explosion or flammability, non-sparking wheel material and special bearings and controls should be considered.
- Corrosive applications: A protective coating or special material, such as stainless steel, fiberglass or plastic may be required if used for corrosive applications.
- Elevated airstream temperature: An awareness of the maximum airstream temperature is required because the temperature affects the strength of fan materials.
Physical limitations
- Inlet size and location
- Outlet size and location
- Fan arrangement/ orientation
- Weight of the fan
- Ease of maintaining the fan
- The physical space available
Drive arrangements
- Power source: All industrial fans require a power source. If electric motors are utilized, a variable frequency drive (VFD) can be used to control fan speed.
- Direct drive: Direct drive ensures a consistent fan speed while offering a more compact assembly.
- Belt drive: The drive ratio allows for adjusting the speed of the fan. The system capacity or pressure requirements may require changes if there are modifications to the process, the hood design, the location of equipment or the air cleaning equipment. With belt driven fans, the motor can be located in a variety of locations/arrangements.
Noise
- Noise: All fans produce a “noise.”
- Sound power & sound pressure: Noise level is measured in units called decibels (db). The noise level will vary depending on the speed, interconnected ductwork and point of operation. The sound pressure is a measurement affected by the fan’s location and other environmental factors.
Contributors to noise:
- The type of fan, flow rate, pressure and fan efficiency contribute to the noise generated by a fan.
- The quietest fans are usually those with a backward impeller design.
- The fans noise level can be increased on any type of fan if the airflow at the fan outlet or inlet is non-uniform.
- Silencers or noise enclosures can be added to fans to reduce noise.
For more information about noise, reference the “ASHRAE Handbook – Fundamentals.”
Safety and accessories
- Guarding: In order to comply with governmental safety requirements, guarding must be included. Danger points to be considered include inlet, outlet, shaft, drive, belts and cleanout doors.
- Accessories: Accessories such as drains, cleanout doors, split housings, inlet boxes and shaft seals can provide assistance in the installation and maintenance of industrial dust collection systems.
Flow control
- Fan accessories: Dampers, variable pitch blades and speed control (VFDs) are three primary fan accessories and assist in managing an industrial dust collection systems flow rate.
- Flow rates: Properly controlled flow rates provide several benefits, including reduced energy demands.
These guidelines are defined in greater detail in the “Industrial Ventilation: A Manual of Recommended Practice for Design.” Additionally, extended information on flow rates and reducing energy demands will be detailed in the blog “Reduce Your Energy Demands with the Right Fan.”
Learn more about IVI’s industry solutions. Contact us today for more information or to start planning your industrial dust collection system.
Resources:
“7.3.1.” Industrial Ventilation: A Manual of Recommended Practice for Design. 26th ed. Cincinnati, OH: ACGIH Signature Publications, 2007. 7-6 – 7-13. Print.